Pneumatic tools, like electronic appliances and hydraulics, are one of the most effective technologies for automation of production processes. Pneumatic technology has been gradually promoted and applied to various industrial sectors, and has played a significant role in production. So how should we identify pneumatic tools during use and how to maintain them? We must do "5 guarantees" when using air tools.
1. Ensure the supply of clean compressed air
Compressed air usually contains impurities such as moisture, oil and dust. Moisture will corrode pipes, valves and cylinders; oil will deteriorate rubber, plastics and sealing materials; dust will cause valve body failure. Selecting a suitable filter can remove impurities in the compressed air. When using the filter, the accumulated liquid should be removed in time. Otherwise, when the accumulated liquid is close to the water baffle, the airflow can still roll up the accumulated material.
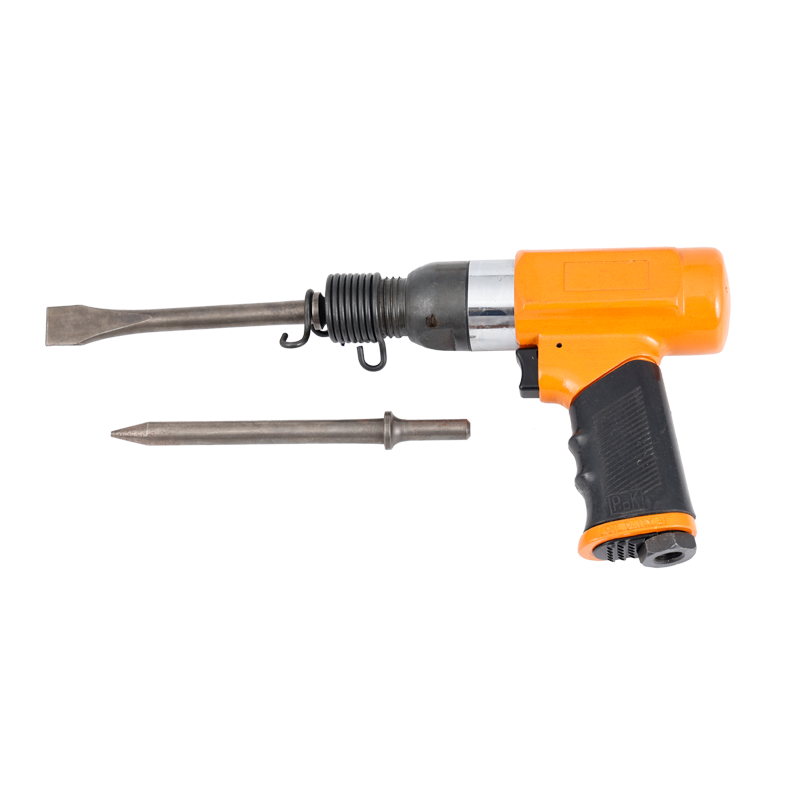
Second, ensure that the air contains an appropriate amount of lubricating oil
Most pneumatic actuators and controls require moderate lubrication. If the lubrication is poor, the following failures will occur: ①Insufficient thrust of the cylinder due to increased frictional resistance and failure of the valve core; ②Air leakage due to wear of the sealing material; ③Damage to components and malfunction due to rust. The method of lubrication is generally to use a lubricator for spray
OVERALL LENGTH 206MM POWER SHORT BARREL ZUODAOAIR HAMMER lubrication, and the lubricator is generally installed after the filter and the pressure reducing valve. Generally, the oil supply of the lubricator should not be too much, usually 1mL of oil per 10m3 of free air (ie 40~50 drops of oil). One way to check whether the lubrication is good is to find a clean white paper and place it near the exhaust port of the reversing valve. If the valve has only light spots on the white paper after three to four cycles of operation, it indicates that Lubrication is good.
3. Ensure the tightness of the pneumatic system
Air leakage not only increases the energy consumption, but also causes the air supply pressure to drop, and even causes the pneumatic components to work abnormally. Severe air leakage is easy to detect when the pneumatic system stops running, and the sound caused by air leakage is easy to detect; for minor air leakage, use the instrument or use soapy water to check.
Fourth, to ensure the sensitivity of moving parts in pneumatic components
The compressed air discharged from the air compressor contains compressor oil particles with a particle size of 0.01-0.08μm. Under the high temperature of the exhaust temperature of 120-220oC, these oil particles will rapidly oxidize, and the color of the oil particles will become darker after oxidation. The viscosity increases and gradually solidifies from liquid to sludge. Such particles below the μm level cannot be filtered out by ordinary filters. When they enter the reversing valve, they will be attached to the valve core, so that the sensitivity of the valve will gradually decrease, and even the action will fail. In order to remove the sludge and ensure the sensitivity, an oil mist separator can be installed after the filter of the pneumatic system to separate the sludge. In addition, regular valve cleaning can also ensure valve sensitivity.
5. Ensure that the pneumatic device has suitable working pressure and movement speed
When adjusting the working pressure, the pressure gauge should work reliably and read accurately. After the pressure reducing valve and throttle valve are adjusted, the pressure regulating valve cover or lock nut must be tightened to prevent loosening.