After the pneumatic wrench is used for a certain time or frequency, the displayed value will appear out of tolerance, which requires the wrench to be regularly calibrated and debugged. From the previous analysis, we can predict that there are two main phenomena in the display value of the wrench:
1. The change of △x causes the overall deviation of the indication value. That is to say, the indication output of the wrench is higher or lower than the nominal value by the same value at each point. The following is the test result of the reworked wrench.
The debugging method is: for the overall offset of the indication value, we can re-align the ruler by turning the adjustment wheel.
2. The output slope of the wrench does not meet the requirements. Taking the NB-100G wrench as an example, when the output low point of the wrench is 30Nm (the low point can be achieved by screwing in or out of the adjusting wheel), the actual output of the wrench has two possibilities, namely the actual output line 1 and the actual output line. Output line 2, ie at 100Nm is either below 100, as in actual output line 1, or above 100, as in actual output line 2.
The debugging method is: adjust a30 to make a3 reach the required value by adjusting the height of the adjusting screw on the lever assembly. (Debugging must be carried out on a torque wrench testing instrument with a flat-blade screwdriver or a hexagon socket screwdriver.) Troubleshooting
It is simply summed up as "one look at two turns and three on stage". "One look" is to see whether the parts of the wrench are complete from the outside, and if they are incomplete, the missing parts should be supplemented; "two turns" is to turn the ratchet wheel and the adjustment wheel by hand to see if it is flexibly stuck. If the rotation is not flexible, there must be a problem ; "Three steps" is to put the torque wrench on the calibrator for testing to see if the indicated value is within the range of
China 1/2 impact wrench the accuracy level, so as to carry out maintenance.
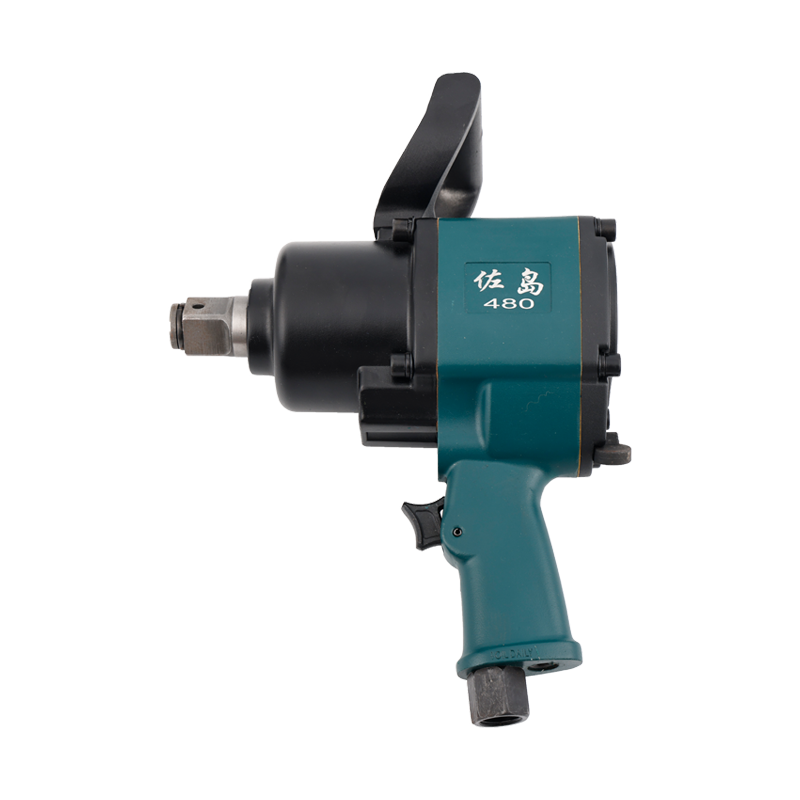
Pneumatic wrenches are generally divided into two categories, one is a conventional impact wrench, which is a very common one, and the other is an impulse pneumatic wrench. The difference between the two is that the former cannot be torqued, while the latter can. Pneumatic torque wrenches fall into the latter category. A pneumatic torque wrench is a torque wrench powered by a high-pressure air pump. It is a torque multiplier with three or more epicyclic gears driven by one or two powerful air motors. The torque is controlled by adjusting the gas pressure. To allow for a specific torque demand setting, each tool is equipped with a dedicated gas-to-torque comparison chart and calibration report. And for further application, the pneumatic torque wrench can be equipped with a torque sensor at the same time to make the output torque more accurate. The air supply can be switched off manually or automatically using a suitable circuit system after the required torque has been achieved. Pneumatic torque wrench is a hand-held rotary pneumatic tool that can precisely set the torque to complete the locking or dismantling of nuts and bolts; the control part is realized by a voltage regulator and a power management system, and the mechanical part adopts a planetary gear reduction mechanism The operation of the pneumatic torque wrench is quiet - less than 85dB(A), with absolutely no impact, reducing damage to the tool, socket and locked object, these two factors can make the tool operator comfortable and reduce Fatigue, improve safety, the maximum torque can reach 300,000N.m. Pneumatic torque wrench provides precise torque control - ±5% repeatability, with sensor + solenoid valve switch, repeatability up to ±2%. Pneumatic torque wrenches are widely used in aerospace, mining, petrochemical, railway, construction, Heavy vehicle assembly and maintenance, heavy equipment loading and unloading and many other fields, especially in product production assembly lines, are widely used, especially where high torque is required. Air Impact wrench, also known as a ratchet wrench and power tool combination , mainly a tool that provides high torque output with minimal consumption. It accelerates the rotation of an object with a certain mass through a continuous power source, and then hits the output shaft instantly, so that a relatively large torque output can be obtained. Compressed air is the most common power source, but there are also electric or hydraulic torque wrenches that use batteries as the power source. Pneumatic wrenches are widely used in many industries, such as auto repair, heavy equipment maintenance, product assembly (usually Known as "pulse tools" and designed for precise torque output), major construction projects, installing wire threaded inserts, and anywhere else a high torque output is required. Air wrenches are available in every standard ratchet socket drive size, from small 1/4" drive tools for small assembly and disassembly, to 3.5".